Vous en avez assez des factures de chauffage qui flambent et des pellets de mauvaise qualité qui encrassent votre poêle ? Comprendre les étapes clés de la fabrication des granulés de bois permet d’éviter les mauvaises surprises. Découvrez comment les matières premières, le séchage et le pressage influencent directement la performance de votre combustible, avec des conseils pratiques pour choisir des pellets fiables et économiques.
L'approvisionnement en matières premières du pellet
La fabrication des pellets repose sur des matières premières issues de l’industrie du bois. On utilise principalement des sciures et copeaux provenant des scieries, menuiseries et parqueteries. Ces résidus, souvent considérés comme des déchets, trouvent une seconde vie en tant que combustible écologique. Cette filière valorise les sous-produits de la première transformation du bois.
Les sous-produits de l’industrie du bois présentent de nombreux avantages. Ils proviennent majoritairement de déchets valorisables sans nécessiter de nouvelles coupes d’arbres. Leur utilisation réduit les déchets industriels et limite l’empreinte carbone. Transformés en pellets, ces résidus deviennent un combustible renouvelable, économique et performant pour le chauffage domestique.
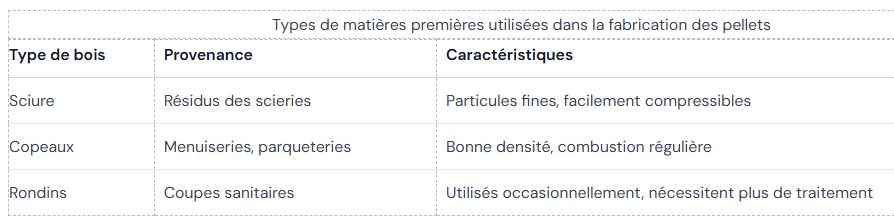
L’approvisionnement local présente des avantages considérables. Il réduit le transport routier et l’empreinte carbone. Près de 84% des distributeurs livrent dans un rayon de 50 km. En Belgique, les fournisseurs locaux renforcent l’économie régionale. Le bois provient généralement à moins de 200 km du lieu d’utilisation.
Le contrôle qualité commence dès la sélection des matières. On vérifie l’absence de traitements chimiques et le taux d’humidité inférieur à 10%. Les certifications ENplus A1 et DINplus garantissent la pureté du produit. Les analyses régulières assurent la constance de la qualité.
Le choix de l’essence de bois influence le rendement. Les résineux comme le pin ou l’épicéa offrent un bon pouvoir calorifique. La résine naturelle agit comme liant lors du pressage. Les feuillus donnent des cendres plus abondantes, moins appréciées pour les poêles.
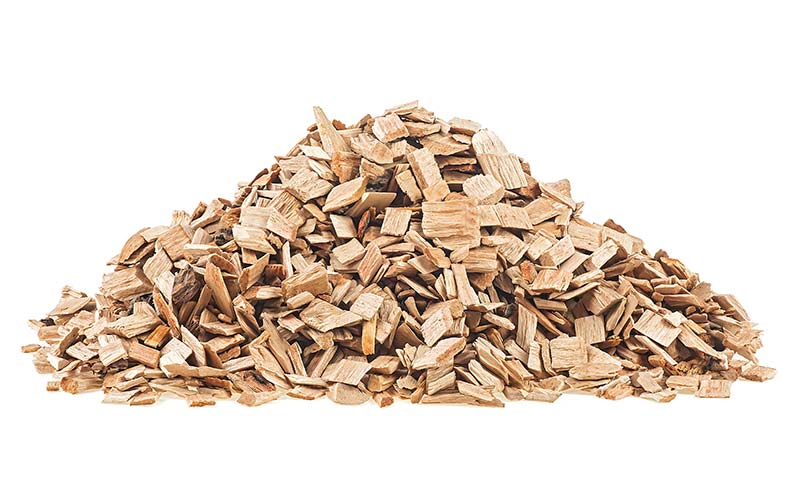
Le séchage : étape importante pour des pellets de qualité
Le taux d’humidité est déterminant pour des pellets performants. Au-delà de 10%, la lignine ne lie plus correctement les particules. L’excès d’eau réduit le pouvoir calorifique et encrasse les appareils. La norme européenne exige moins de 10% d’humidité pour garantir un bon rendement énergétique.
Le tambour sécheur est une installation rotative inclinée. La matière circule par gravité sous l’effet d’air chaud. Les modèles rotatifs atteignent 80% d’efficacité thermique. Ils économisent 20% de combustible par rapport aux systèmes classiques. La température est strictement contrôlée pour préserver la qualité du bois.
Les usines valorisent leurs propres déchets comme source d’énergie. Des résidus comme l’écorce alimentent les chambres de combustion. Ce système réduit les déchets et l’empreinte carbone. L’énergie produite alimente le séchoir, créant un circuit énergétique vertueux.
Plusieurs paramètres influencent la qualité du séchage. Le taux d’humidité initial détermine la durée du processus. La température doit correspondre aux caractéristiques du bois utilisé. La conception du séchoir affecte l’efficacité énergétique. Enfin, ventilation et débit d’air contrôlent l’évaporation de l’eau résiduelle.
Un séchage inadéquat diminue le rendement énergétique. Chaque point d’humidité en trop réduit de 2% le pouvoir calorifique. Les granulés humides brûlent mal, encrassent les chaudières et produisent plus de cendres. Un taux d’humidité maîtrisé assure une combustion propre et économique.
Des sondes intégrées mesurent en continu l’humidité des granulés. Les séchoirs rotatifs permettent un contrôle précis des paramètres. Les fabricants visent un taux final entre 10 et 12%. Des analyses régulières assurent la constance du produit. Ces systèmes automatisés évitent les variations qui dégradent la qualité finale.
L'affinage de la granulométrie pour une compaction optimale
La réduction en particules fines facilite la compaction. Avant le pressage, le bois est transformé en sciure homogène. Cette étape garantit un mélange uniforme des fibres. Une granulométrie adaptée assure une meilleure adhésion des particules durant le pressage.
Le broyeur à marteaux utilise des percussions répétées pour décomposer le bois. Les marteaux rotatifs broient les copeaux en sciure fine. Ce système traite jusqu’à 8 tonnes par heure. La granulométrie finale varie entre 2 et 15 mm pour des résultats optimaux.
La taille des particules influence la densité finale des pellets. Des fibres trop grossières affaiblissent la cohésion. Les granulés de diamètre 6 à 8 mm atteignent 650-700 kg/m³. Une structure homogène réduit les fissures et améliore le rendement énergétique.
Les mesures s’effectuent via des analyseurs d’image dynamiques comme le CAMSIZER X2. Celui-ci capture 300 images par seconde pour une précision micrométrique. Les tamis rotatifs trient aussi les particules à raison de 20 à 50 tonnes/heure selon le calibrage.
Un affinage rigoureux maximise l’efficacité des presses. Les particules inférieures à 6 mm évitent les blocages. Les marteaux tournant à 2500 tr/mn garantissent une répartition uniforme. Ce travail préparatoire diminue l’usure et augmente la production.
Une granulométrie irrégulière cause des défauts de compression. Les particules trop épaisses génèrent des pellicules poreuses. Les presses subissent une surcharge mécanique avec des matériaux non homogènes. Les certifications exigent une longueur inférieure à 40 mm pour éviter ces problèmes.
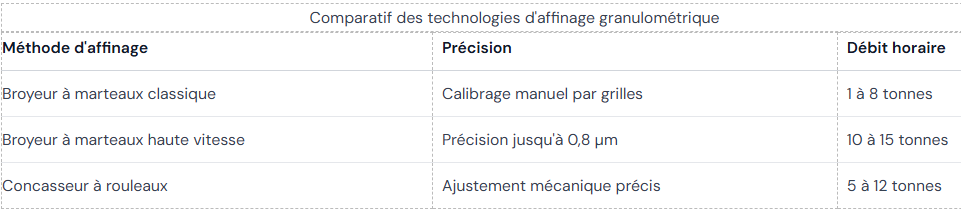
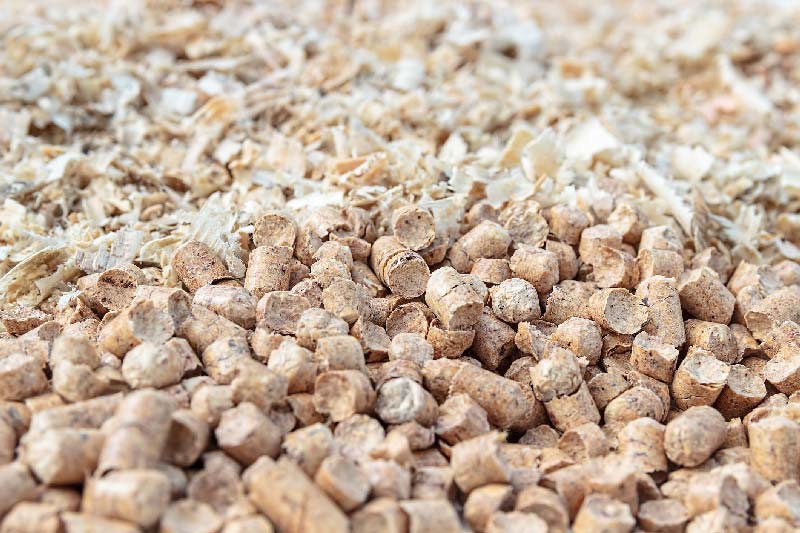
Le pressage : formation des granulés de bois
La presse à pellets comprime la sciure sous haute pression. La matière est chauffée à 60-80°C pour activer la lignine. Les granulés sortent par des trous calibrés de 6 à 8 mm. Ce processus exige une matrice en acier résistant à l’usure. La pression atteint 500-700 kg/m³ pour une densité optimale.
La lignine agit comme un liant naturel. Sous chaleur (60-80°C) et pression, elle durcit en refroidissant. L’absence d’additifs chimiques préserve la pureté. Les certifications ENplus A1 excluent les produits synthétiques. Seule la résine naturelle du bois assure la cohésion. La qualité dépend du taux de lignine dans le bois utilisé.
Les presses appliquent 500-700 kg/m³ de pression. La température interne varie entre 60 et 80°C. Ces paramètres activent la lignine sans dégrader la matière. Les modèles industriels fonctionnent en continu. Les presses à matrice annulaire offrent un rendement supérieur. La pression uniforme garantit un produit homogène et résistant.
Les additifs naturels restent exceptionnels. Ils incluent parfois des cendres de bois (max 0,2%). Les certifications limitent ces ajouts à 2%. Les fabricants évitent les traitements artificiels pour préserver la qualité. Les pellets premium contiennent moins de 0,1% d’additifs. La norme DINplus exige 100% de matières naturelles.
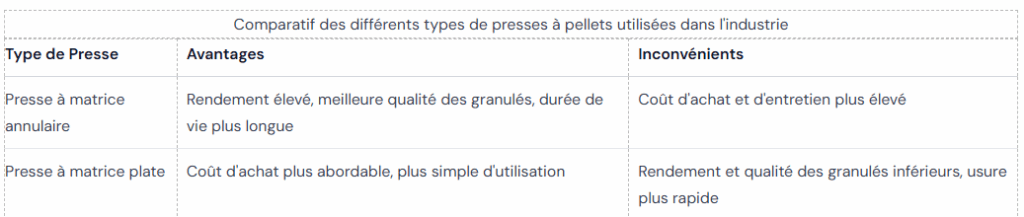
Le pressage influence directement le pouvoir calorifique. Une densité de 650-700 kg/m³ maximise l’énergie libérée. Les granulés bien comprimés dégagent 4,6 kWh/kg. Une structure poreuse réduit le rendement. Les certifications garantissent un minimum de 4,5 kWh/kg. La compaction optimale évite les pertes d’énergie.
Refroidissement et tamisage : finalisation des granulés
Le refroidissement stabilise les granulés après pression. Les pellets sortent à 90-100°C. Un refroidissement par air soufflé garantit leur solidité. Sans cette étape, la chaleur altère leur structure. Une température maîtrisée assure un stockage sans dégradation.
Les refroidisseurs à contre-courant optimisent le processus. L’air froid circule à l’opposé des granulés chauds. Les modèles Intecso traitent 0,3 à 8 tonnes par heure. Cette méthode homogène la température. L’échange thermique maximal limite les variations.
Le tamisage élimine les poussières et fines. Ces résidus encrassent les poêles et chaudières. Un taux de fines inférieur à 1% est requis. Les tamis rotatifs extraient les impuretés. Cette étape prévient les coûts de réparation.
Les fines récupérées sont réutilisées comme combustible. Elles évitent le gaspillage industriel. Certaines usines les recyclent dans les séchoirs. D’autres les valorisent en énergie. Ce circuit fermé maximise l’efficacité.
Ces étapes définissent la qualité finale. Des granulés refroidis et tamisés passent les certifications ENplus A1 et DINplus. Les normes exigent moins de 10% d’humidité. La Belgique privilégie les produits 98% purs.
- Taux d’humidité initial : influence la durée de refroidissement
- Température du séchoir : adaptation aux caractéristiques du bois
- Conception du refroidisseur : impact sur l’efficacité énergétique
- Ventilation et débits d’air : contrôle de l’évaporation résiduelle
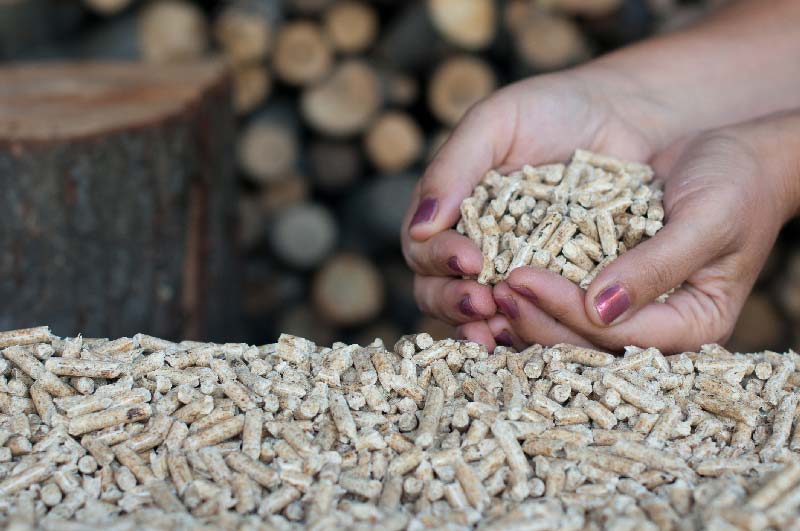
Le conditionnement des pellets
Le conditionnement garantit la qualité jusqu’à l’utilisation finale. Les sacs de 15 à 18 kg facilitent le transport et le stockage. Les palettes filmées de 1,2 à 1,5 tonne assurent une livraison sans dommage. Un emballage hermétique prévient l’humidité, préservant le pouvoir calorifique. Les fabricants certifiés évitent les sacs poreux qui dégradent le produit.
La logistique de livraison respecte les contraintes des particuliers. Les fournisseurs sérieux déposent les palettes au plus près du garage ou de la chaudière. Les camions à basculement automatisé évitent les manipulations manuelles. Les délais de livraison moyens varient entre 3 à 5 jours ouvrables. Les systèmes de suivi en temps réel rassurent les utilisateurs sur l’heure d’arrivée.
Les certifications encadrent les normes de stockage. Les normes ENplus A1 interdisent les entrepôts humides. Les silos métalliques ou les sacs triplés couches préservent la qualité. Un stockage en environnement sec évite les agglomérats inutilisables. Les particuliers vérifient systématiquement la date de fabrication sur les emballages.
Les innovations simplifient la manutention pour l’utilisateur. Les vraciers automatiques déversent les pellets directement dans les silos. Les systèmes de convoyage extractible servent les espaces exigus. Les sacs ergonomiques à ouverture rapide évitent la poussière. Les distributeurs réactifs remplacent les lots endommagés sans frais supplémentaire.
Le conditionnement influence le choix des utilisateurs. Près de 65% des clients préfèrent les palettes filmées anti-rouille. Les sacs en polypropylène résistent mieux à l’humidité que le papier kraft. Les fournisseurs locaux proposent des formats adaptés aux chambres de stockage type. La clarté des mentions guide les décisions d’achat.
La traçabilité complète rassure les acheteurs exigeants. Les codes-barres indiquent la date, l’usine et les certifications. Les fabricants sérieux communiquent sur les contrôles qualité en amont.
La fabrication des pellets repose sur trois piliers : choix rigoureux des matières premières, séchage optimisé et pressage précis. Chaque étape influence directement la performance et la durée de combustion. Pour un hiver serein, misez sur des granulés bois certifiés ENplus A1 ou DINplus : qualité garantie, factures réduites, et chaleur durable à domicile.
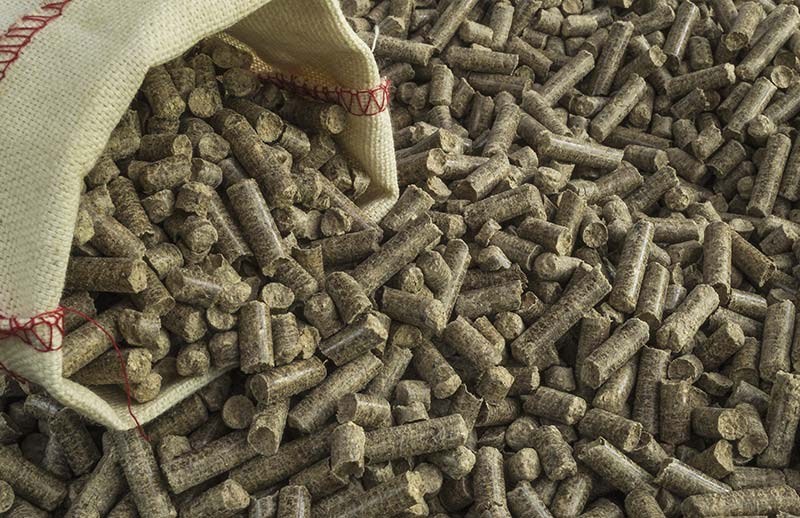
FAQ : Les étapes clés de la fabrication du pellet de bois
La rentabilité de fabriquer ses propres pellets dépend de plusieurs facteurs. Il faut prendre en compte le coût de l’équipement (presse et broyeur), la consommation d’énergie, le prix des matières premières, et le temps que vous y consacrerez. Si vous possédez déjà un broyeur, la rentabilité sera plus rapide.
Bien que la production de pellets puisse générer des revenus, il est important de considérer le coût des matières premières (sciure de bois), les frais de transformation (broyage, séchage et fabrication), le conditionnement et le transport. En 2022, le surcoût de production d’une tonne de granulés était de 100 à 120 €.
Il n’y a pas de « meilleur » bois universel, mais certains critères permettent de déterminer la qualité des pellets. Que ce soit du bois vierge ou du bois résineux, privilégiez un combustible avec une faible teneur en humidité (inférieure à 10 %) et sans additifs chimiques. Les certifications comme EN plus A1 ou DINplus sont un gage de qualité.
Pour choisir des pellets de qualité, vérifiez leur densité et leur dureté. Ils doivent être compatibles avec la taille de votre poêle et avoir un pouvoir calorifique élevé (environ 5 kWh/kg). Une faible teneur en cendres (inférieure à 0,7 %) est également préférable pour un entretien plus facile.
Le tamisage des pellets est essentiel pour le bon fonctionnement de votre poêle. Il permet d’éviter l’encrassement causé par la poussière et les fines, ce qui pourrait diminuer le rendement de votre appareil et noircir la vitre. En éliminant ces résidus, vous prolongez la durée de vie de votre poêle.
En plus de prévenir l’encrassement, le tamisage protège les composants du poêle, notamment la vis sans fin, dont le remplacement peut être coûteux. Une combustion plus homogène et efficace est également favorisée, ce qui permet d’éviter une surconsommation de combustible et de maintenir les performances de chauffage.